
One can face some dilemmas when the time comes to decide upon which part, system, or facility to reuse when several options are available. The decision-making process should be based on the evaluation of a certain number of parameters which should not be exhaustive, and should be carefully reviewed and adapted to the context in which reusability is done. Some of drivers of the decision-making process of reusability would be:
- Fixed and variable costs (traditional accounting misleading)
- Performance and Capability
- Behaviour, and interface with other parts
- Modularity (How flexible is the design?)
- Customer acceptance and satisfaction
- Underlying technology competitiveness
- Capacity availability
- Cost of incremental capacity
- Fixed costs and Variable costs, as for parts and systems reusability
- Manufacturing Flexibility: Volume/Mix flexibility, Product/Changeover flexibility
- Process capability (Is the process delivering what it is expected to deliver? How consistent
- Reuse effectiveness index.
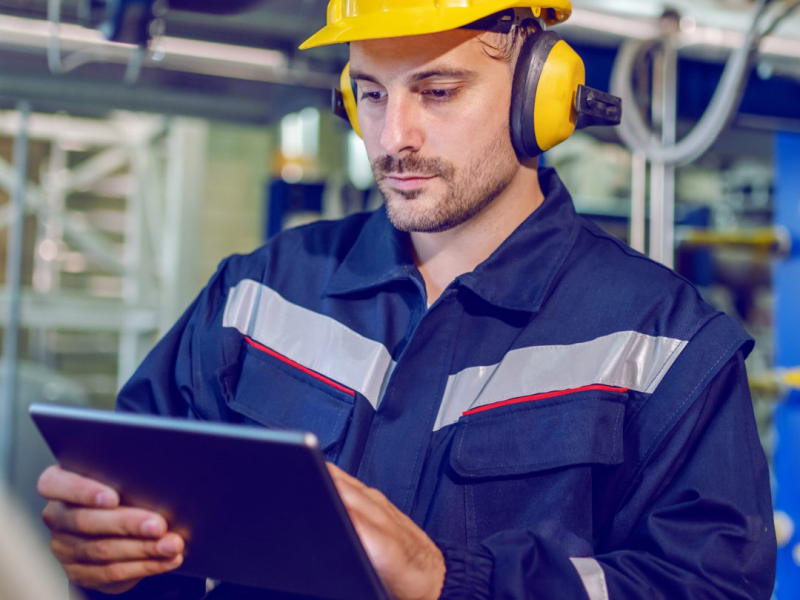
XX%
XX%
XX%
Reduction in Manufacturing Costs
XX%
XX%

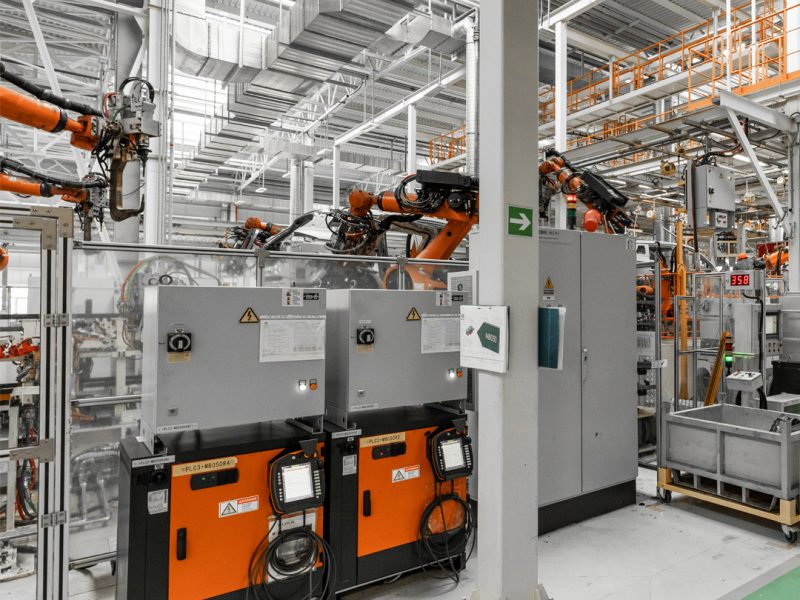
- Easier Work Management – provide the ability to define operational practices as digital workflows provides ease of operation
- Consistent user experience on any device
- Complete collaboration to coordinate people and/ or applications in a consistent and governed manner
- Deploy Modular approach provide the ability to deploy the “right-sized” solution to meet specific business needs
- Standardise operational work practices across a manufacturing enterprise
- Centrally develop and manage corporate standards for MES/MOM functions and applications
- Enable Multi-Site Changes & Agility – provide the ability to evolve the solution to meet changing business needs across a manufacturing business unit/sites

MIGNITED have expertise in Manufacturing Execution System in functions to efficiently manage and document operational processes and material flow in industrial manufacturing plants which can be scaled to individual needs or incrementally implemented for faster return on investment and alignment with business priorities.
- Production Management – digital information and rules management for work order dispatching and tracking for any combination of manual or automated equipment job execution.
- Inventory Operations Management – real time tracking of materials, semi-finished and finished products including receiving, transfers or for managing Kanban inventory as materials are consumed and products are made.
- Bill of Material and Recipe Management – Quality losses can be minimised and consistency improved through enforcement of product and process specifications.
- Track and Trace – Reduce the cost of regulatory compliance and protect brand equity with automatic electronic record keeping for detailed product genealogy and end to end material traceability in minutes.
- Data Store for Reporting and Continuous Improvement – detailed manufacturing history as performed vs. planned offers drill down analyses into operational performance and identification of improvement potentials.
- Enterprise Integration – Integration with Enterprise Resource Planning enables agile, short-term production management and provides schedule flexibility and adoption for the plant as well as supply chain visibility into operations and inventory.
- Quality Operations – Automate and enforce quality inspection and data collection procedures in alignment with the real-time status of work order and job execution, and in response to shop floor events for reducing giveaway and variance in production results.
- Plant Performance Management – Unlock more value and capacity from existing assets with visibility into line and plant equipment utilisation and Overall Equipment Effectiveness (OEE) KPI’s.
- Digital Workflow Management – Automate operational activity and data collection processes, eliminating paperwork and manual error-prone
procedures. - Empowerment and Mobility – Empower the modern workforce with a digital and mobile user experience and keep them connected with mission-critical processes on and offline.